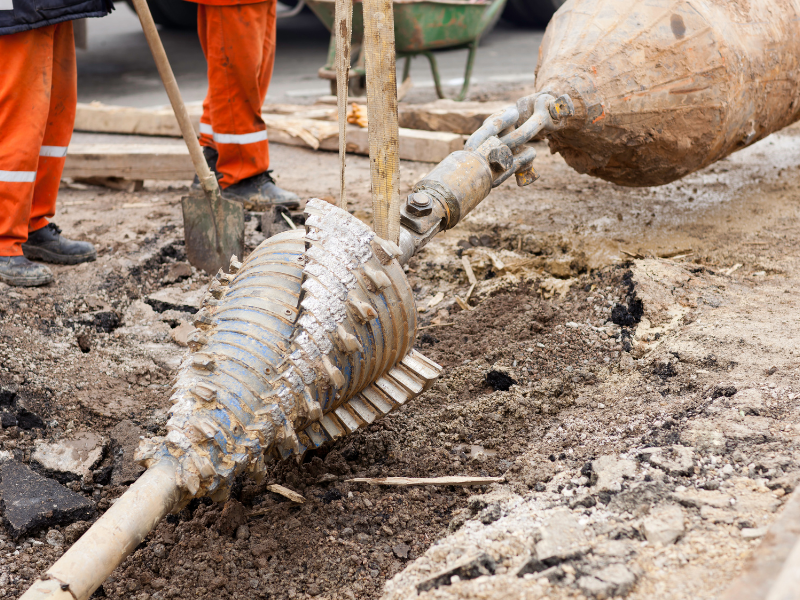
Every boring contractor’s objective is to be profitable. To achieve this goal, the project must be efficient and must be completed within an acceptable time frame. These objectives require proper planning, skill and experience on the part of those in charge and of those on the project who operate the machinery and a variety of other tools.
From a contractor’s point of view, there can be little benefit in any failures of equipment or tooling. Disclosed industry tooling failures do lead, however, to the discovery of alternative procedures for achieving future drilling success.
Tooling failures are often the result of unusual or complex conditions which arise from unknown hazards — hazards that do not occur in directional drilling. Other failures are frequently the result of practices in the production process. Experience, for which there is no substitute, is key in directional drilling. As with other professional endeavors, expert drill use depends on knowledge and skill, which is developed over time.
Mud motors in high PSI applications are important in horizontal drilling. The following are five suggestions in production processes for maintaining efficiency in the use of mud motors in the directional drilling process of resource extraction.
First, avoid stalling the motor, as a motor stall usually indicates that the fluid flow has stopped motor rotation. This can be the result of increased thrust while in contact with the rock or cutting face, preventing motor rotation. This type of motor stalling forces fluid through the rotor and stator assembly without any rotation, which in turn leads to damage of both the motor and the pump.
Second, minimize abrasives in the fluid as much as possible by keeping all screens clean and in good condition. Effectiveness is a function of tolerance between motors and other equipment like the stator. All abrasives in this process are moving at high pressure through the motor, causing wear, reducing torque and, ultimately, overall productivity.
Third, be prudent by performing maintenance on a weekly basis or at around 100 hours of use, for the simple reason that moving parts in motors wear out. Sometimes it may seem that budget or production timetables demand foregoing scheduled maintenance. Remember, though, that horizontal directional drilling equipment usually breaks at the wrong time and repairs can be very costly. Most breakdowns can be prevented with methodical maintenance; it rarely pays, in the long run, to skip it. Productivity depends on teamwork and on the collective operation of men and the equipment they use. In drilling, and especially in horizontal and directional drilling, this includes a myriad of parts: bearings, rotor, stator, etc. Usually, if maintenance is not performed weekly or after only a hundred hours or so, the equipment’s full effectiveness will diminish and costs of service will rise. If the machinery malfunctions or breaks as a result of insufficient maintenance, the cost will be even greater.
Fourth, remember that projects may appear profitable when worked out on paper, but that profitability on a busy highway or other potentially dangerous work site is another matter. When a hazardous project is already over budget and past its completion time, with others waiting impatiently for the job to be finished, profits can drop or evaporate altogether. There are instances in which tooling has justifiably been sacrificed to finish the bore, just to get the project done. These are not situations, however, that anyone finds satisfactory or profitable in the end.
There are many cases in which effective practices actually increase the crew’s productivity and lower expenses in completion, while reducing tooling costs of the total holes drilled. These are the processes that incorporate the previous suggestions for proven success in running directional drilling over the long haul.